Standards EN 8 and EN9 steels have been the most favored choices among metallurgists because of the superior mechanical properties as well as versatile applications these steels possess. Both the materials could be put to various applications, but quite contrary specifications like composition, mechanical properties, and applicability differ from one another. Such differences should be very well understood so that one can make an informed decision, particularly in industries where the direct impact of material performance rests on operational efficiency and cost.
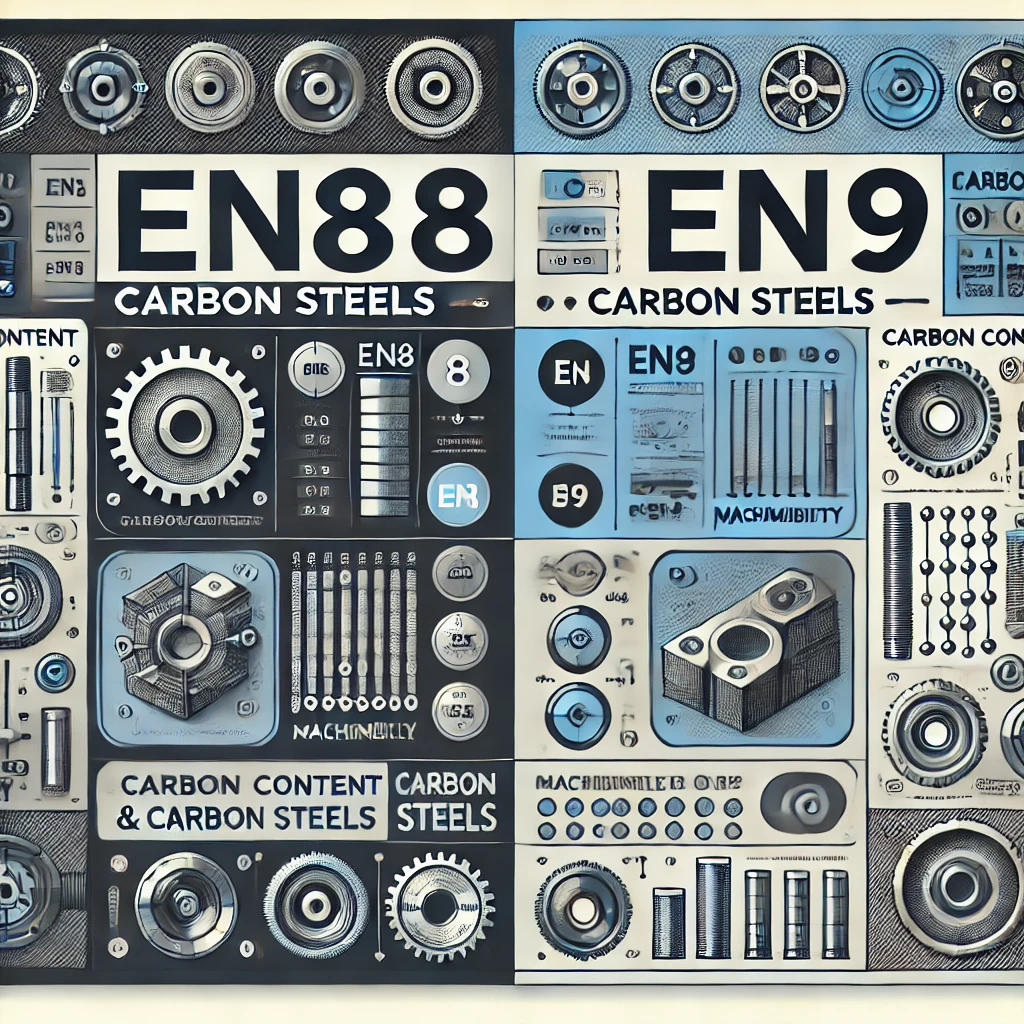
What is the Material EN 8?
EN 8 is a medium strength carbon steel that is used all over for general engineering. It is normally supplied either normalized or rolled and possesses really good values of tensile strength and toughness.
Salient features of EN 8:
- It is medium carbon steel and has an approximate composition of 0.35% to 0.45% carbon.
- It is suitable for machining, drilling, and welding with proper heat treatment.
- It has high wear resistance, making it ideal for parts like shafts, studs, and bolts.
- It finds applications in industries such as automotive, construction, and machinery manufacturing due to its reliability and abundance.
EN9 Material- What is this?
EN9 is the great next level of Carbon Steel, which is mainly used at the place where higher hardness and strength are required as compared to that of EN 8 material. Its carbon content is about 0.50 to 0.60 percent; due to which it becomes valuable for wear resistance after heat treatment.
Key Properties of EN9:
- This will create high hardness due to high carbon content.
- Good materials for uses which have highly impact or wear usage like crankshafts and gear.
- Less machinable than EN 8, but yields much greater durability as a heat treatment.
- EN9 has exceptional toughness and tensile strength that make it one of the important materials in the region of the industry dealing with heavy-duty.
Among EN 8 and EN9, the main distinctions are as follows:
First, carbon content: EN 8 has lower carbon content (0.35%–0.45%) than that of EN9 (0.50%–0.60%) in which both results in hardness and strength difference.
Machinability: Second, EN 8 is easier to machine than EN9 so it has more importance in the research field because they have a factor of very general engineering. Even, EN9 is tough but has a special requirement to machine.
Applications: EN 8 is recommended for medium-duty applications such as shafts and bolts, while EN9 is employed for heavy-duty applications such as gears and crankshafts.
Heat Treatment: If we look at the heat treatment, EN9 sees greater benefits than EN 8 because EN9 attains higher hardness levels than EN 8.
EN 8 Material Price in India
The EN 8 material price in India is based on various factors like the demand of the market, cost of raw materials, and costs of operations. EN 8 steel generally costs lesser compared to EN9 due to lower carbon content and the fact that it is easier to manufacture.
Latest Market Trends: EN 8 materials are currently priced in the range of approximately ₹50-₹65 per kg in India. These prices, however, are subject to change depending on global demand and the effects of supply chain disruption.
Regional Variation: Prices vary regionally in India; industrial cities like Pune and Chennai provide competitive options.
Price of En9 Compared to Other Materials
EN9 steel is, therefore, expected to be relatively more expensive than most grades of steel. For this reason, the price of EN9 steel usually hovers between ₹65 to 85 per kg in India. Because of its higher percentage of carbon content, and the extensive process it undergoes to improve its mechanical properties, this additional cost is attached to it.
Price Predictions for Steel in India Affect EN 8 and EN9 Prices
Steel price predictions in India determine the pricing of EN 8 and EN9 materials. Various factors influence the steel price in India such as:
Market Fluctuations in the Global Arena: The domestic prices are affected directly by the oscillations in the global steel market as a result of the supply-demand method.
Costs of Raw Materials: The cost of iron ore and coking coal, which are required for steel production, either raises or lowers the EN9 material and EN8 material prices, respectively.
Government Policies: Pricing trends are impacted by tariffs, export-import duties, and incentives offered to the steel sector.
Recent Trends in Steel Prices in India
Reducing Global Demands: Reduced global demand has led to a trend in steel consumption down, with steel prices stabilizing and reducing.
Technological Advancement: Enhanced costs in manufacturing steel items would bring down the end costs of materials such as EN 8 due to innovation in the steelmaking processes.
Low-Carbon Steel Initiatives: Low-carbon development policies have started to affect the industry with recycled steel as an alternative.
When it comes to choosing between the 2 materials, you should note that for each application, different material specifications are necessary.
Select the EN 8 if your project demands excellent machining, moderate strength, and high cost-efficiency.
Choose the EN9 for the application where the resistance to wear, tensile strength, and toughness against aging are of importance.
Conclusion
Both EN 8 and EN9 are carbon steels familiar in any industry, each bearing its own significance. The EN 8 material price is lower than that of EN9; therefore, the EN 8 material can be used for more purposes in general engineering. EN9 is costlier because it gives better hardness and strength. With the ongoing fluctuations in steel prices and a growing emphasis on environmentally sustainable manufacturing, it should not be surprising that understanding the material properties and market trends impact both economic prudence and cost-effective decision making in businesses.
In following through into the steel price prediction in India, these companies will be able to have foresight into price changes and determine the best route for optimal procurement. Source materials for machinery or construction: EN 8 or EN9 selection has to depend on the specific technical and economic considerations of a given project.